Is there a difference between PFI and GDI?
Port Fuel Injection vs. Gasoline Direct Injection
As automakers around the world have been tasked with delivering more fuel-efficient vehicles, a multitude of design improvements have been put in place to provide consumers cars with improved efficiency. One technological advancement involves the deployment of a modified engine configuration that has been widely adopted: Gasoline Direct Injection (GDI).
Historically, the most widely produced internal combustion engines were of the Port Fuel Injected (PFI) design, where the fuel is sprayed into the intake ports to mix with incoming air. In fact, many new vehicles are still manufactured with this engine design. The fuel injectors in PFI configurations are typically mounted in the intake manifold and the air/fuel mixture is pulled into the cylinder head as the intake valve opens.
Click on the images above to enlarge.
In a GDI engine, the fuel injectors are situated in the cylinder head and fuel is sprayed directly into the cylinder where the air / fuel mixing then occurs.
There are many advantages of the GDI system over the PFI design, the most significant of which is its better fuel economy.
The graphics below depict the rapid growth of the GDI technology globally, increasing from 1 to 44% of engine production in the last 17 years, and forecast to increase to 62% in the upcoming five years.
Another advantage is performance, with increased power delivered from a system that combines higher injection pressures and more accurate delivery of fuel into the piston cylinders. Combustion occurs when gasoline vapors mix with oxygen, and in GDI systems, the fuel sprayed into the cylinder is more finely atomized allowing for a nearly instantaneous ignition. The sophisticated computer controls in these direct injected systems enable multiple injections and metering of fuel which aid in both performance and efficiency of the vehicle.
To see a GDI combustion chamber in action, view the video below :
The fuel systems in the GDI engines require a higher level of sophistication in their hardware selection: fuel injectors that can withstand higher temperatures and pressures and high-pressure fuel pumps. The fuel injectors are typically designed with multiple holes that aid in the delivery of precise delivery of fuel into the cylinder and the injector placement is also critical to the efficiency of the system. The injectors can be side mounted or mounted at the top-dead center of the cylinder, depending on the spray pattern desired, and effecting the overall fuel efficiency of the vehicle.
To further support increases in performance, many of the GDI engines are combined with a turbocharger, allowing for even more power delivery. Turbochargers use the cars exhaust gases to propel a turbine that powers an air compressor which forces increased levels of oxygenated air into the cylinders, allowing for a higher rate of fuel burn. The use of turbochargers, in tandem with direct injection technology, is increasing in light duty vehicles, with forecasted growth projected by global automakers.
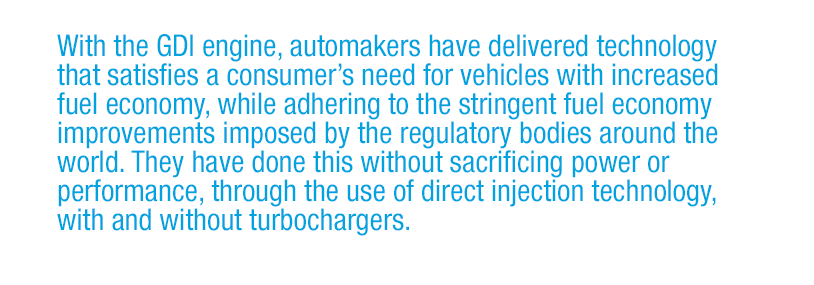
The rapid adoption of this technology by car manufacturers and its forecasted growth in new vehicle production, assures that GDI vehicles will quickly become a sizeable percentage of the car parc in every region of the world.