How HDEO is Responding to Changing Hardware Trends
Commercial vehicle (CV) engine hardware has evolved significantly over the last three decades in order to respond to the global focus on emissions reduction and fuel economy requirements. Heavy Duty Engine Oils (HDEO) must evolve and anticipate these trends to meet current and future performance demands.
Here we look at 5 of the key changes seen in CV engines and HDEO over the past 3 decades and what this means for engine oils and vehicle operators.
Trend 1: Increased power density
On-road CV engines have not grown in engine size, but power output has risen with the utilization of hardware components such as turbochargers.The turbocharger helps to increase the power density of the engine by generating more power per combustion cycle. However, use of the turbocharger also brings the challenge of higher operating temperatures within the engine, which can peak at about 3000C.
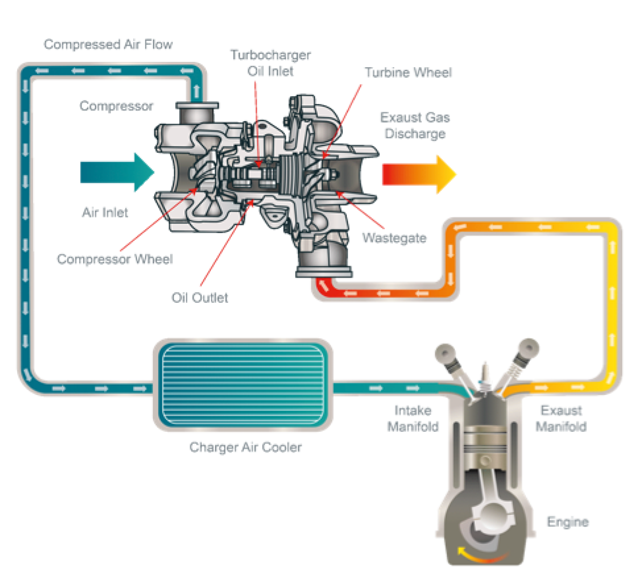
©Afton: How turbochargers work
Therefore, to reduce downtime and lower the Total Cost of Ownership (TCO), CV operators should look to select an engine oil which will minimise the performance impact and help maximize engine durability. To do this, the engine oil should be resistant to oxidation at high temperatures as well as keeping the turbocharger cool and clean of carbon and varnish deposits.
Trend 2: Hardware material changes
OEMs have had to respond to emissions-reducing and fuel economy legislations while supporting engine durability and keeping costs down. The result is a number of new materials used in CV engine manufacture, which shapes the engine oil.Lead-free bearings have reduced toxicity and also minimise the risk of corrosion in the engine, helping extend oil drain intervals - although they are more costly.
Steel piston heads can withstand higher temperatures and pressures than aluminium. Using steel means redesigning the piston head to optimize combustion and adding oil channels for better cooling.
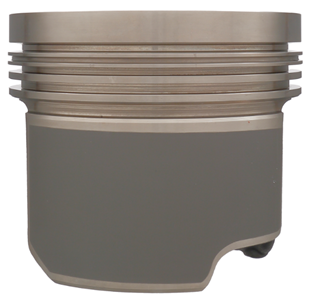
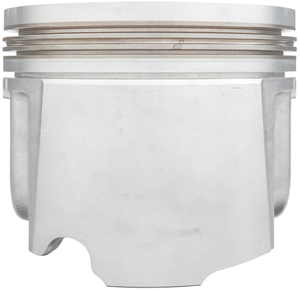
Steel (Left) vs Aluminium (Right) HD diesel engine piston heads
New coating materials on components like piston rings and bearing shells help reduce friction and improve fuel efficiency. There are many coating types and the engine oil must support all of them for fuel savings to be realized.
However, new materials bring compatibility challenges, limiting the additive chemistries that can be used in the engine oil. However, as these bearing and coating materials are well suited to the lower viscosity oils that improve fuel economy, these lubricant solutions are more future-proof.
Trend 3: Aftertreatment systems evolution
Exhaust aftertreatment technology has evolved significantly since Euro IV in 2004 where predominately only exhaust gas recirculation was utilized. Fast forward to 2021 where a combination of aftertreatment systems are used to achieve targets required by stricter emission legislation - increasing the manufacturing complexity and cost of the vehicle.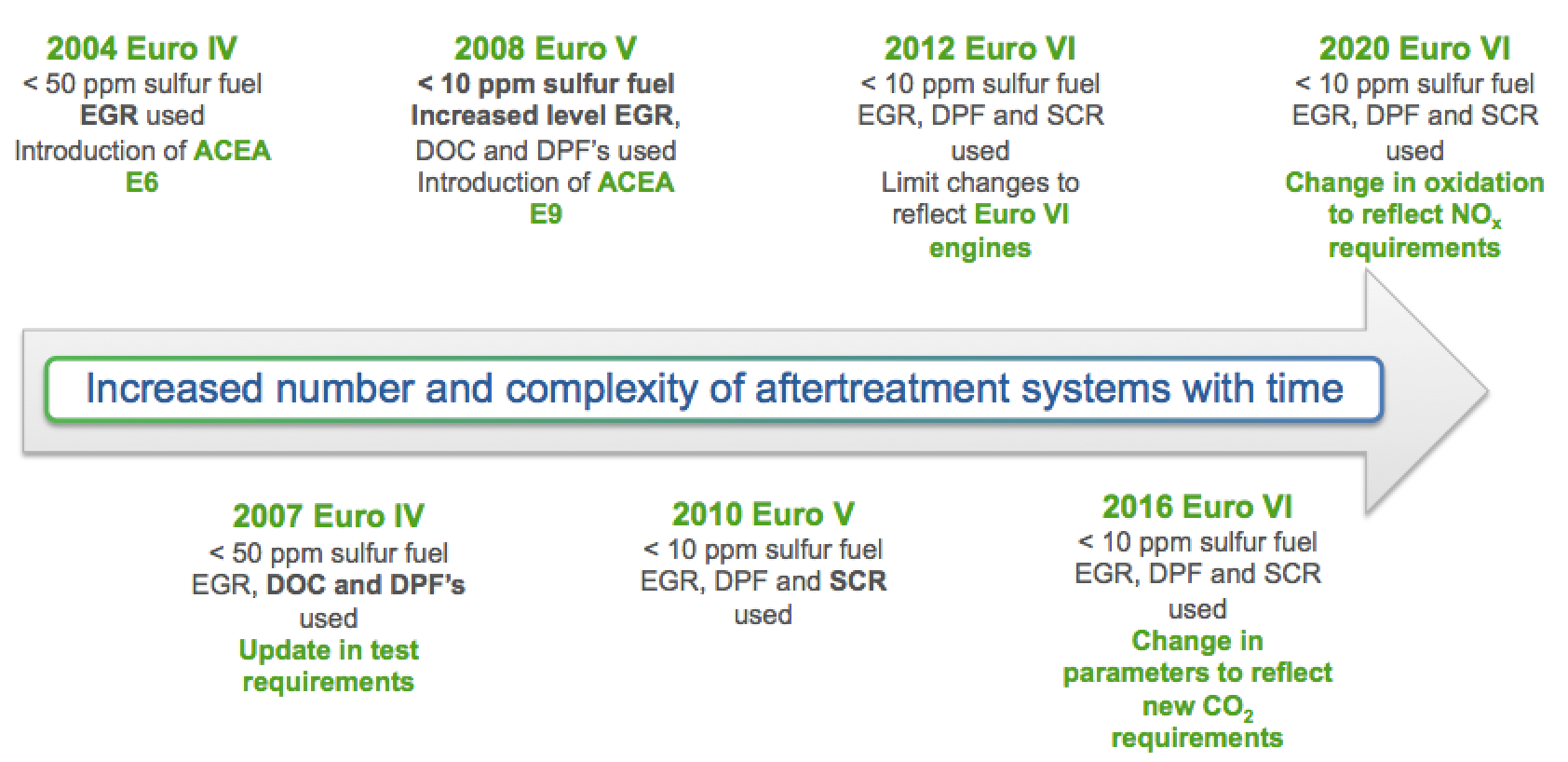
© Afton: The evolution of exhaust aftertreatment systems
Although costly, a combination of aftertreatment systems have to be fitted to achieve emission requirements as each play a slightly different role.
Exhaust gas recirculation (EGR) reduces NOx by re-introducing exhaust gases into the combustion chamber, lowering the combustion temperatures. However, as this can lead to soot build up and acid generation in the engine oil, the oil must offer good detergency, dispersancy and oxidation control.
Diesel oxidation catalysts (DOC) and diesel particulate filters (DPF) both reduce particulate matter (PM). Both systems are sensitive to sulfated ash, phosphorus and sulfur (SAPS), to varying degrees. This limits the type and amount of additive chemistries that can safely be used in the engine oil while still maintaining engine protection and fluid durability.
Selective catalytic reduction (SCR) reduces NOx with a chemical reducing agent, commonly called Urea, which was introduced in 2010. Engine oils must not only be compatible with this agent but also themselves be resistant to oxidation.
Due to the sensitivity and cost of replacing equipment, it is crucial that operators consider a reduced SAPS engine oil designed for modern aftertreatment systems.
Trend 4: Extending oil drain intervals
While engine oil requirements have been changing, Total Cost of Ownership (TCO) pressures have also been pushing OEMs towards longer periods between engine oil changes – adding to the already considerable demands on the oil.At the same time, fuel economy considerations are driving engine oil viscosity lower and lower, making protection from wear more challenging.
Over time Iveco, MAN and Daimler have tripled the distance between oil changes from 50,000km to 150,000km. Daimler is targeting as high as 200,000km under approved and monitored conditions. Most OEMs do make allowance for more severe operation though and specify shorter drain intervals under such conditions.
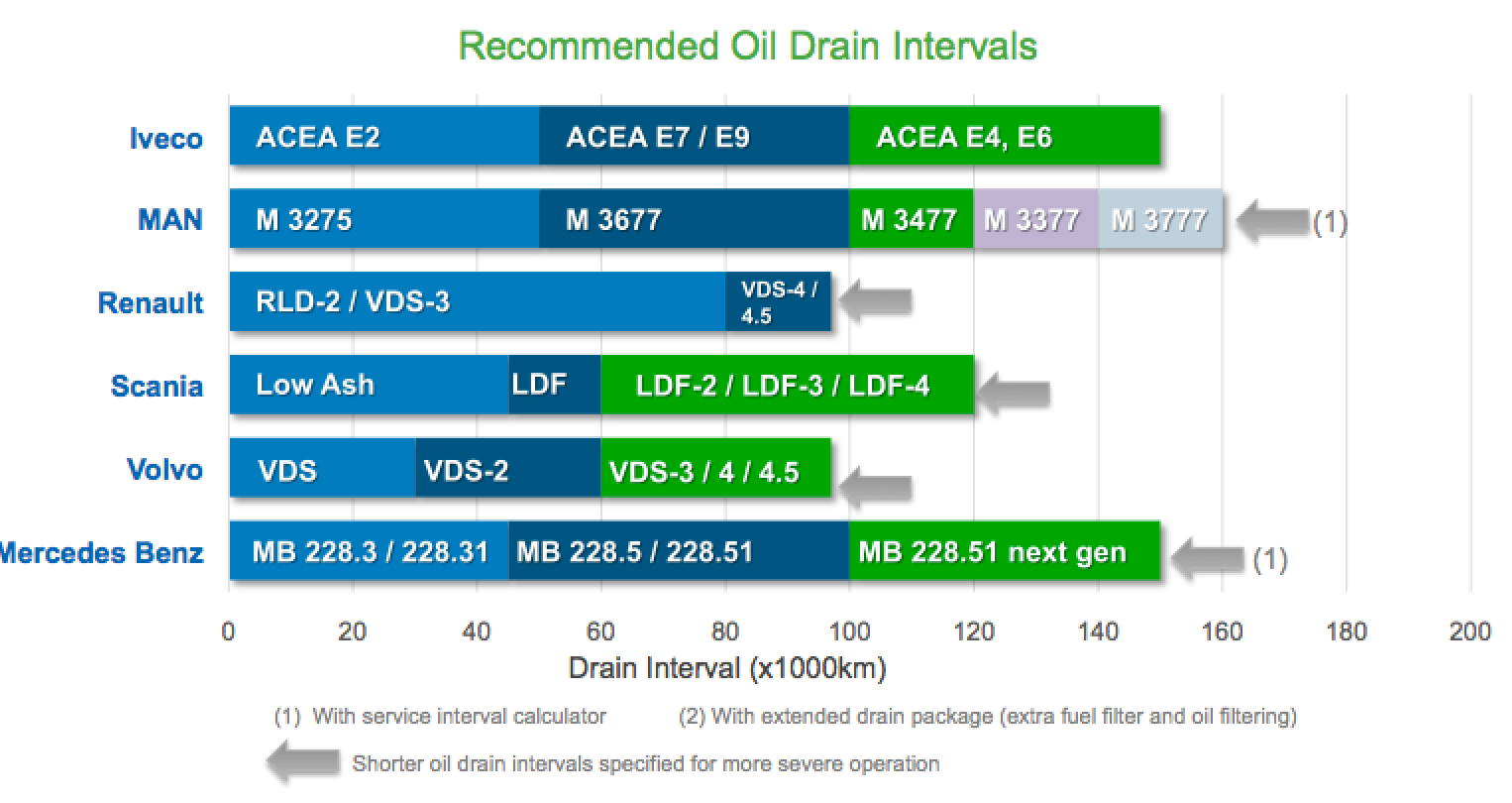
Operators of more modern CVs need to look for engine oils offering reliable engine protection by maintaining excellent oxidation control as well as lowering TCO through improved fuel economy and operating over a greater distance.
Trend 5: Off Road operation severity
Off Road vehicles are subject to less stringent emissions legislation than On Road CVs. Although this means less restriction on additive chemistries, the engine oil needs to cope with a far wider variety of applications.From modest capacity backhoe loaders to huge 59L blocks in mining haul trucks, Off Road engines vary wildly in size and all experience more severe operating conditions.
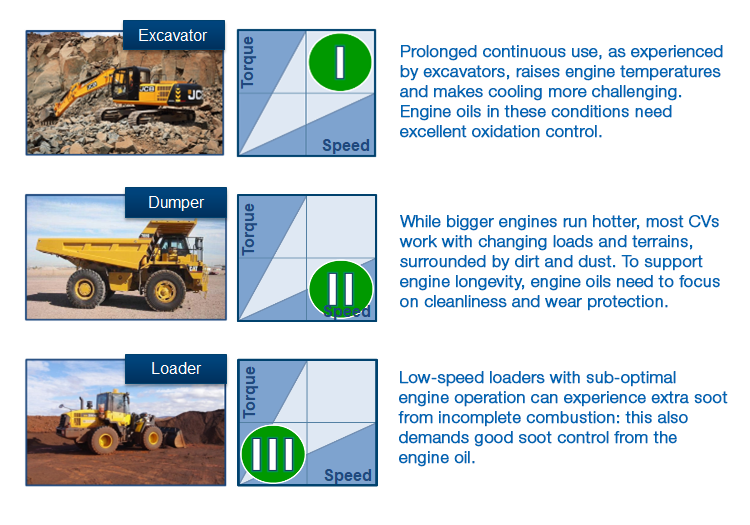
What do operators need to consider?
The influence of emissions, fuel economy and TCO on vehicle hardware and HD engine oils is greater now than at any point in the last 30 years.CV operators now, more than ever, need to consider whether their choice of HD engine oil can support their particular combination of engine hardware, exhaust aftertreatment systems, oil drain intervals and operating conditions.
Formulating oils that offer durable engine protection, using lower viscosity fluids and with restrictions on SAPS level, is a challenge – but one that Afton has always been well placed to address through the development and use of innovative additive technologies.
Afton’s close partnership with OEMs offers the clearest view of the road ahead: ensuring that our HDEO additives portfolio delivers the right performance for each CV application – both now and for the technologies and materials of the future.